SelectSeal Max200
Horizontal Form-Fill-Seal • Rollstock Thermofomer
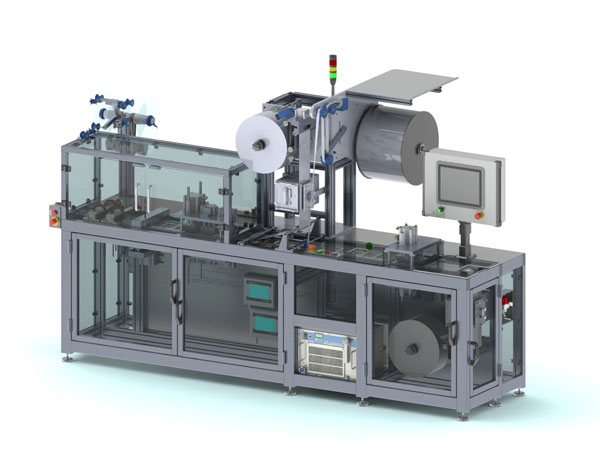
Application
For High volume, low SKU sterile barrier packaging applications where space savings is critical. Ideal for clean room device manufacturing and for flexible or rigid rollstock web widths up to 200mm.
Packaging Materials
Rollstock forming and non-forming
Forming Films: PET, PETG, HIPS, PVC, Poly, Nylon/Surlyn ®
Non-Forming Films: Heat sealable Tyvek ® , Medical Paper, Poly Films or Paper board.
- Modular, adaptable design allows varied packaging sizes and features
- Simple tool change. No water, wiring or reheating required.
- Class 7 cleanroom compatible
- Open software architecture, native software files included
- Allen-Bradley CompactLogix Processor with 12” PanelView Plus color touchscreen
- Recipe scan to load with auto tool verification
- Fully validatable, GMP Compliant
- Technical Support
- Installation and Setup
- Maintenance
- Training
Machine Specifications
Typical Configuration | Other Configurations | |
---|---|---|
Max Web Format (web width x index) |
8” x 8” (203mm x 203mm) | Larger format readily available |
Max Draw Depth | 3.0” (76mm) | |
Max Film Thickness | 30 mil | |
Rollstock | 14” (356mm) max dia roll, 3” (76mm) core | Larger diameter roll unwind options available |
Rate | 3 – 20 Cycles per minute (CPM) | |
Materials of Construction |
Anodized Aluminum Extruded framework, SS, other cleanroom compatible materials |
|
Power | 240VAC or 480VAC, 3phase, 60hz | Other voltages available |
Air Consumption | 80-100PSI air source, CFM to be provided based on actual application |
|
Film Unwinds | Powered, constant tension with low roll, web break and splice detect as standard |
Dual roll unwind or cart |
Preheat Station | Contact heat on both sides of film | |
Forming Station | Vacuum form with air assist; Male vent seam plug with vacuum; Male plug assist |
High force cold forming (foil) |
Load Station | Modular length per application for manual or auto load |
Operator load indicators |
Top web print | Brake stretch eyemark registration for pre-printed top film |
All print technologies can be provided |
Seal Station | 3700# capacity servo based sealing station with direct force load cell feedback for verification. |
Pneumatic driven sealing available |
Cutting | Cross cut knife (XMD) with Crush Cut (MD) | Matched metal, steel rule or forged type |
Controls | Allen-Bradley PLC and HMI with Yaskawa motion | Other platforms available upon request |
Safety | Zero tolerance safety package | |
Vision | Cognex or Keyence cameras for inspection of device presence or graphical print verification. |
|
Software Features | Process parameter verification, 4 User security logins, Data change tracking, Line Clearance |
Customizable per requirements |